Qualità dei gioielli
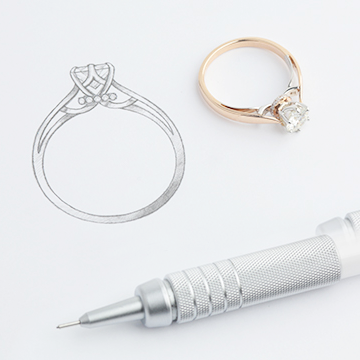
Progetto
La prima persona a "vedere" l'idea del designer è un foglio bianco su cui l'idea assume contorni grafici. Per uno studio dettagliato e la creazione di un disegno tecnico, fondamentale per le successive fasi di produzione, lo schizzo viene trasferito al computer e, utilizzando una tavoletta grafica e una penna, perfezionato.
Modellazione 3D
Il disegno tecnico creato dagli artisti finisce nelle mani dei designer 3D, che dimostrano notevole creatività creando un modello tridimensionale della decorazione con un software professionale. I modellatori al computer lavorano a stretto contatto con gli artisti per trasmettere appieno il loro intento.
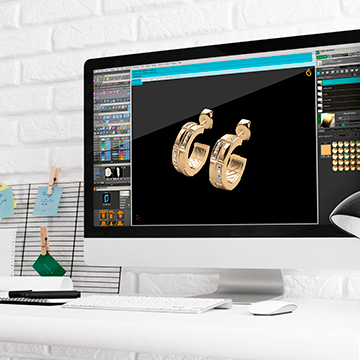
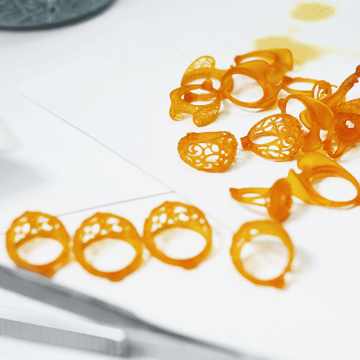
Prototipazione
Un file informatico contenente il modello di un gioiello sviluppato dai designer 3D viene trasferito alla fase di prototipazione. Il futuro gioiello viene "coltivato" su una speciale stampante 3D in polimero o cera. Il modello creato con la macchina viene poi finalizzato dallo stilista per la successiva fusione.
Modellazione
Indipendentemente dal metallo con cui è stato concepito il gioiello, esso appare inizialmente in argento. Molti prototipi vengono applicati su barre di cera e fusi in metallo. Dopo la rifinitura finale da parte dello stilista, diventano un modello principale, un prototipo della futura circolazione dei gioielli.
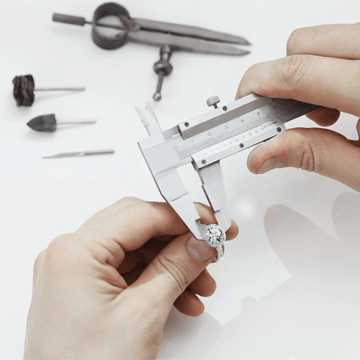
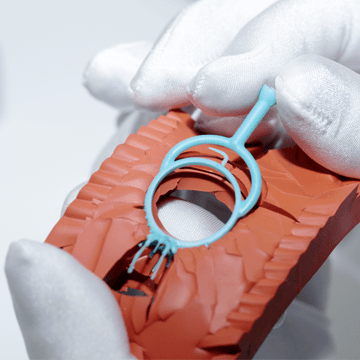
Realizzazione di stampi
Il modello master viene utilizzato dai gioiellieri per ottenere uno stampo. Il prototipo viene immerso in una speciale massa di plastica, modellato e inviato in un forno, dove ad alta temperatura la massa, simile alla plastilina, si indurisce fino a raggiungere lo stato di gomma. Lo stampo viene tagliato con cura e il modello master viene rimosso.
Modellazione in cera
Il modellatore di modelli a cera persa serra saldamente lo stampo, nel quale la cera fusa viene colata sotto pressione, assumendo la forma del futuro prodotto e indurendo all'istante. I prototipi di gioielli vengono posizionati su una barra di cera, ottenendo un pezzo grezzo per la fusione, simile a un albero di Natale.
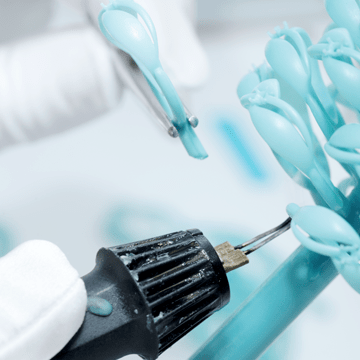
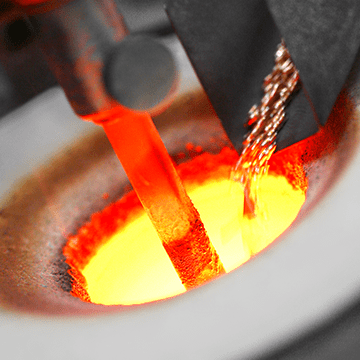
Fusione
Il tuorlo di cera viene posto in uno stampo speciale, un cilindro, che contiene la massa per lo stampo e il materiale necessario. Il gesso si indurisce e i modelli in cera si fondono. Il cilindro viene rimosso, lasciato raffreddare e poi riempito con la lega per gioielli. Dopo la fusione, la massa solida dello stampo viene lavata via e l'albero di Natale in metallo viene illuminato. I prodotti vengono tagliati e inviati alla lavorazione speciale.
macinazione
I prodotti appena fusi sono opachi e privi di lucentezza. La molatura conferisce al metallo una certa purezza e una certa dimensione superficiale. Con l'aiuto di una macchina molatrice, il maestro "raccoglie" il metallo in eccesso. Per elaborare i dettagli più piccoli, si utilizza uno strumento manuale: un trapano per la lavorazione degli ugelli o una lima.
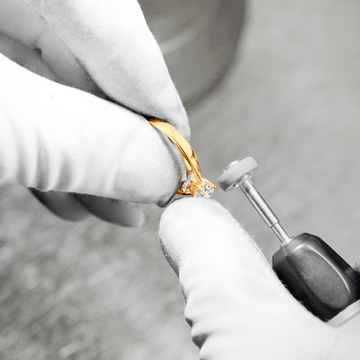
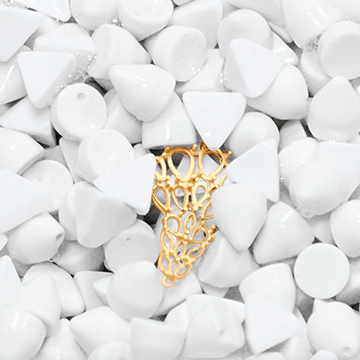
Burattatura e lucidatura
I prodotti vengono posizionati in tamburi rotanti con speciali agenti lucidanti o reagenti. Solitamente, la burattatura prevede due fasi: levigatura a umido e lucidatura a secco. Gli specialisti caricano e scaricano i prodotti, monitorando il tempo: è importante impostare correttamente i parametri dell'attrezzatura e non danneggiare il metallo.
Montare
I gioielli più complessi vengono inviati al sito di montaggio. Qui si uniscono le parti decorative e la chiusura degli orecchini, si fissano gli anelli ai pendenti, si assemblano i bracciali più complessi e si eseguono molte altre operazioni. La resistenza dell'assemblaggio viene verificata dal controllo qualità.
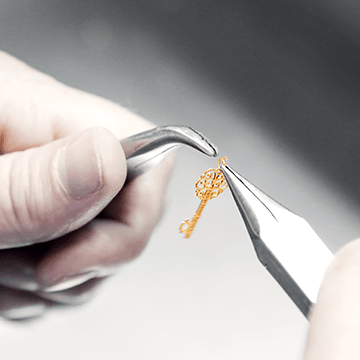
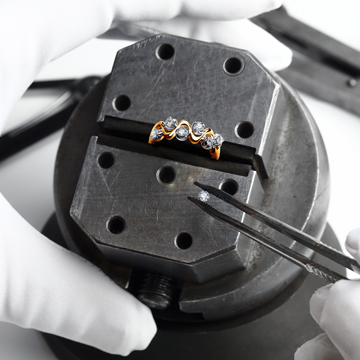
Incastonatura di pietre
Una delle fasi più laboriose e impegnative della produzione. Specialisti esperti lavorano al microscopio, posizionando con cura gli inserti – dagli zirconi ai diamanti – su apposite piattaforme e fissandoli. In questa fase, lavorano professionisti con molti anni di esperienza e tutte le pietre vengono applicate esclusivamente a mano.
Galvanizzazione
I gioielli in metallo bianco sono ricoperti di rodio nobile, un metallo del gruppo del platino. I prodotti vengono immersi in un bagno galvanico, dove, a seguito di una reazione chimica, vengono ricoperti da uno strato uniforme di metallo. Sui prodotti in oro rosso, il rodio viene applicato con una matita speciale, di norma, nei punti in cui sono applicati gli inserti.
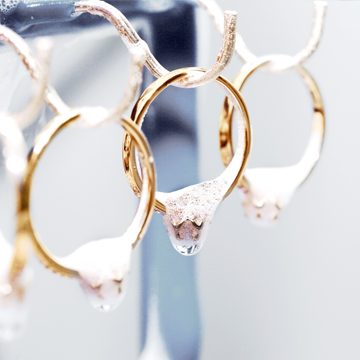
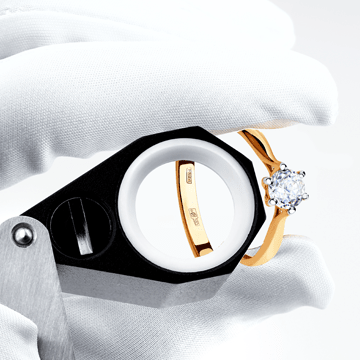
Controllo finale
Nella fase finale, i gioielli vengono attentamente controllati dal servizio di controllo qualità. Solo i prodotti che soddisfano rigorosi standard ricevono il marchio ESNOLA, che è un certificato di decorazione. Successivamente, i gioielli vengono inviati alle gioiellerie partner.